(廣州鑫昇工程塑料有限公司技術開發部提供)
【摘要】利用模具脫模進行材料成型的一個主要問題是制品脫模時通常會粘住模具。由此帶來的問題是在成型過程后,制品粘住表面后,形成模具“結垢”并破壞模具,制品本身的質量也受到很大影響,因此脫模劑的使用就很有必要,但是傳統的脫模劑也存在一定的劣勢,所以本文將通過分析脫模劑的作用及其劣勢,介紹一種進階版的“脫模劑”——脫模母粒,分析其成分和使用。
【關鍵詞】脫模劑 脫模母粒 性能
一、脫模劑的作用
在設計和制造任何預成型部件,如金屬、橡膠、塑料或復合材料,模具脫模劑都是必不可少的。脫模劑作為一種涂料使基體具有非常低的表而能。當應用于制造特殊部件模具的基體材料上時,這些脫模劑形成微米級厚度、熱穩定的膜層,它和模具表面形成化學連接,可以讓成型部件快速輕易脫落。好的脫模劑能產升復合、無垢的脫模效果,因而降低生產成本,減少因清理模具和修補表面缺陷所耗費的時間。
當采用新的模具材料和樹脂系統組合開發零部件時,選擇正確的脫模劑是其重要的環節。選擇正確的脫模刺將減少制造周期,保證成型部件表面質量的一致性,可大限度地避免在上漆或粘接之前所需的后處理工藝(拋光)。脫模劑不能含有任何影響后產品晶質或者成型后處理效果的成分。成型部件必須能順利干凈的脫模,固化前則不會脫模。脫模產晶針對所采用的生產工藝還必須具備成本效益。脫模劑令人滿意的特性包括以下幾點:
(1)簡單的應用步驟;
(2)短暫的干燥時間:
(3)模具上無殘留;
(4)不轉移到成型部件:
(5)耐高溫:
(6)多種脫模性;
(7)極少量氣味;
(8)環保、健康和安全標準正越來越支持在生產過程中使用無溶劑(水基)脫模技術。
二、傳統脫模劑的劣勢:
由于脫模劑本身的性質各方面,每一類脫模劑不可少地存在一些缺點,下面將逐一簡要分析。
①溶劑型脫模劑:不甚環保。與非溶劑型脫膜劑相比,對人體健康(揮發性有機化合物)和安全(火災隱患)影響較大。
②水性脫模劑:制造工藝技術更為復雜。實現良好的胎面成膜難度更高。此類脫膜劑更易出現穩定性問題,也易受生物侵害。與溶劑型脫膜劑比,水性脫膜劑蒸發量較低,不適合室溫下的脫膜操作或周期時間較短的操作。由于模具問題和操作時間的影響,水性脫模劑的使用范圍還是有限制的,比如北方,冬天,并且模具沒有加溫裝置,就不實用。
③無溶劑型脫模劑:如涂敷不當可導致粉塵危害。需使用特殊涂敷設備(通常采用靜電噴槍),故噴涂成本較高。采用無溶劑型脫膜劑時可能還需對模塑設備進行改動,確保模具能夠達到熱平衡。這些因素往往限制了無溶劑型脫膜劑的應用。
④犧牲型脫模劑:涂敷過量易在模具壁面上形成結垢。如過量涂敷或脫膜劑的化學性能與模塑成型后加工工藝(噴涂、粘接等)不匹配時,脫膜涂層通常會部分轉移到成型部件上,給后加工工藝造成不利影響。如采用水性產品則易使模具冷卻,帶走系統的熱量與能量(除非工藝專門針對此類情形設計,否則此性能會造成操作不便)。
⑤半型脫模劑:需對操作工人進行更多培訓,確保正確的補涂頻率。為使首次涂敷的半性脫膜劑能充分作用在模具表面,必須確保模具清潔干凈。
⑥內部脫模劑:隨著時間推移會不斷轉移到表面,影響模塑成型后加工工藝(粘接與噴涂)或成品表面美觀。由于內部脫膜劑有時不能轉移到模具界面上或無法確保的脫膜效率,因此一般還需要外部脫膜劑予以輔助。
三、“進階版”脫模劑——尼龍成型脫模多功能母粒
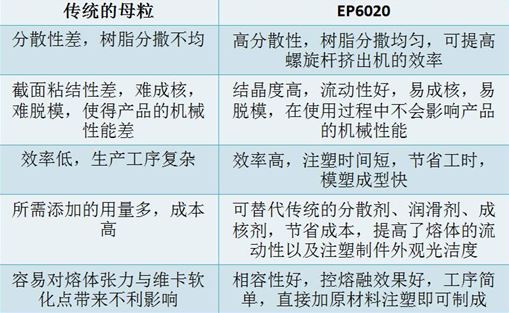
1. 產品介紹
一種用于聚酰胺(PA)材料生產加工的綜合母粒;它是由內潤滑(成核)劑、外潤滑(脫模)劑、抗氧化(穩定)劑、高分散性尼龍樹脂作載體混合而成的顆粒狀產品;在注塑制件時具有改善產品流動性、能快速成型、注塑加工易脫模、提高尺寸穩定性及表面光潔度;
2. 產品特性:
3. 產品原理:
①尼龍成型脫模多功能母粒是內潤滑劑(提高化學分子成核結晶度)、和外潤滑劑(保持順暢脫模)、抗氧劑(保持加工穩定)、相結合的多功能成型助劑包;
②具有非常強的極性中心和很長的非極性碳鏈其結構在極性上與塑料相容的部分起內潤滑、提高結晶度成核劑的作用,良好的外潤滑性、保持能順暢脫模;
③把在極性上與塑料不相容部分的內潤滑(化學性結晶成核)與外潤滑(物理性加工成型)合為一體的作用;
4. 產品參數:
項目 |
數據 |
單位 |
滴點 |
210 |
℃ |
密度 |
1.14 |
g/cm3 |
粘度 |
2.3 |
— |
應用 |
尼龍(PA6/PA66) |
-- |
5. 使用方法:
根據物性要求,兼顧成本效益,添加量在 0.8-1.5% 之間。
一般情況如下:
◆尼龍(PA6\PA66)樹脂注塑添加0.8-1.5%(攪拌)
◆尼龍(PA6\PA66)生產改性添加0.8-1.5%
本文章由廣州鑫昇工程塑料有限公司技術開發部提供